55 Mejores prácticas y consejos de expertos en preparación de pedidos en almacén
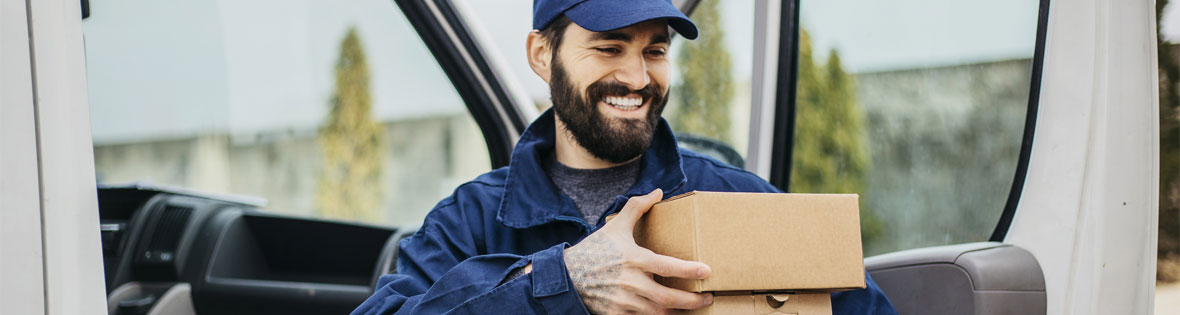
Hay muchos procesos entrantes y salientes involucrados en el movimiento y la gestión del inventario que conforman la disciplina de la gestión del almacén. Las empresas a menudo se centran en los procesos de salida para aumentar la satisfacción del cliente y reducir las ineficiencias operativas y los costos.
Pero la preparación de pedidos es una parte crucial de la parte de salida de la gestión del almacén. Constituye todos los pasos involucrados en la recuperación física de los artículos almacenados en el almacén para cumplir con el pedido de un cliente.
Importancia de mejorar la preparación de pedidos en el almacén
Las empresas inteligentes buscan mejorar la preparación de pedidos por una buena razón:es la actividad más costosa y que requiere más mano de obra en el almacén. generalmente representa más de la mitad de los costos operativos del almacén.
Las mejoras en la preparación de pedidos ayudan a las empresas a entregar los productos adecuados a los clientes más rápido, y gaste menos dinero en los pasos asociados. Los selectores de pedidos de almacén generalmente toman una lista de selección y viajan a diferentes lugares del almacén para obtener los artículos. búscalos en las estanterías del almacén, extráigalos y haga coincidir el papeleo para garantizar la precisión del pedido antes del envío.
La parte más lenta del proceso de preparación de pedidos es viajar, que ocupa el 55% del tiempo del selector de almacén, de media, seguido de trámites y otras actividades (20%), buscar (15%) y extraer (10%), según una investigación del Instituto de Logística y Cadena de Suministro de Georgia Tech. Por esta razón, gran parte del trabajo en torno a la mejora de los procesos de preparación de pedidos tiene como objetivo reducir el tiempo de viaje improductivo.
Lograr la mejor preparación de pedidos en su clase requiere saber dónde están los productos, exactamente cuántos hay disponibles, saber cuántos necesita, de modo que no esté seleccionando cada pedido individual de uno en uno, y asegurarse de que estén ubicados estratégicamente para facilitar la selección y el procesamiento rápidos para el envío.
Entonces, ¿cómo pueden las empresas minimizar el tiempo de preparación de pedidos al tiempo que garantizan el cumplimiento preciso de los pedidos y la seguridad de los empleados en un almacén?
55 consejos para la preparación de pedidos en almacén y mejores prácticas para adoptar
Dado que no existe una única forma de garantizar pedidos perfectos, hay muchos métodos, herramientas y procesos que una empresa puede emplear para mejorar la preparación de pedidos. La combinación de estrategias, las mejores prácticas y tecnologías que su organización debería adoptar dependerán de la industria, número de artículos vendidos y velocidad a la que el inventario se mueve a través de los almacenes.
Observar el diseño del almacén y los métodos de preparación de pedidos utilizados dentro de sus cuatro paredes ayudará a una empresa a seleccionar los procesos adecuados. tecnologías y equipos para mejorar la preparación de pedidos.
Consejos de diseño de almacenes para la preparación de pedidos
La excelencia en la preparación de pedidos comienza con la elección del diseño y el flujo de almacén adecuados para su estrategia de procesos comerciales.
-
Elija un tipo y flujo de almacén. Los almacenes generalmente están diseñados para mover mercancías en uno de los diseños siguientes (o alguna combinación de ellos).
- Flujo en forma de U coloca los muelles de recepción y despacho en el mismo lado del edificio, y los productos se mueven en forma de U desde la recepción hasta el envío. Este diseño ofrece espacio de acoplamiento compartido y, por lo general, es mejor para edificios pequeños.
- Flujo en forma de I coloque la recepción en un extremo y el envío en el otro extremo del edificio para que todas las mercancías se muevan en una sola dirección. Un flujo en forma de I es bueno para empresas de gran volumen, así como aquellos que necesitan un fuerte control de seguridad sobre las mercancías que entran y salen del almacén.
- Flujo de almacén en forma de L tiene descarga entrante en un extremo y envío saliente en un ángulo perpendicular a esa área. Esto puede facilitar el cross-docking, cuando los artículos se retiran de un camión y se cargan inmediatamente en otro. Esto es bueno para las empresas que nunca almacenan productos en racks, enviando stock poco después de traerlo.
-
Decida cómo se organiza el producto dentro de ese flujo. Esto podría ser lo que se llama un diseño de almacén triádico, que se divide en tres zonas:movimiento rápido, Producto de movimiento medio y lento. En los almacenes que no utilizan este diseño, el producto no está dividido en zonas. Muchos almacenes adoptan un diseño en el que automatizan una sección con los artículos adecuados y aún tienen personas involucradas en la recolección de artículos, hasta cierto grado, en el otro.
- Coloque los productos que se mueven más rápido lo más cerca posible del cumplimiento para que sean fáciles de elegir.
- Almacene los artículos que a menudo se venden juntos uno cerca del otro.
Métodos de preparación de pedidos de almacén
Si no tiene un método de recolección, estará seleccionando para cada pedido cronológicamente sin visibilidad de los otros pedidos en su cola; esto lleva a perder mucho tiempo atravesando el almacén para recuperar el mismo artículo a lo largo del día.
-
Las operaciones con un volumen de pedidos bajo o que venden productos pesados o de alta gama deben ser discretas, selección de pedidos individual, picking de piezas o picker-to-part. Este es el método de preparación de pedidos más sencillo, en el que una persona elige el pedido completo, caminando por el almacén, tirando de todos los elementos necesarios y, a menudo, consolidándolos en un contenedor.
-
Para organizaciones que necesitan recoger y empaquetar pedidos de varios artículos rápidamente y tienen una gran cantidad de SKU y selecciones por pedido, la selección de olas es una buena opción. La recolección se realiza en oleadas programadas, y todas las zonas se seleccionan al mismo tiempo. Los artículos se clasifican en sentido descendente a medida que se preparan para envíos individuales. Agrupe los lugares de picking, como los pedidos, en base a reglas predefinidas, y los libera para que se cumplan juntos, de modo que los recolectores puedan elegir para toda la ola al mismo tiempo.
-
Para aumentar la eficiencia del picking, los trabajadores pueden recolectar en lotes donde recolectan para varios pedidos, como artículos similares o artículos ubicados en áreas similares, en un solo viaje. Para empresas con pocas selecciones por pedido, la recolección por lotes puede reducir el tiempo de viaje. El operador entra en el almacén, recoge la cantidad total de artículos necesarios y luego los asigna a cada pedido individual.
-
Para grandes almacenes con muchos SKU, la selección de zonas es a menudo ventajosa. El picking por lotes puede incorporar el método de picking por zonas, en el que un selector se encarga de cuidar una determinada zona del almacén, obtener todos los artículos para su zona y luego pasar el pedido. Por esta razón, La selección de zonas también se conoce como selección y pasada. Los elementos pueden moverse, por ejemplo, a lo largo de una cinta transportadora hasta que todos los elementos necesarios estén en la caja.
-
Las empresas innovadoras están probando sistemas de clasificación y configuraciones amigables con las personas para aumentar la eficiencia del proceso de selección. El selector de almacén permanece en un solo lugar, y los productos son llevados al selector por un transportador, un dispositivo robótico o alguna otra tecnología automatizada. Piense en el trato amable como si automatizara el proceso de selección discreto.
-
Otra forma de reducir el tiempo de viaje es el pick-to-box. Pick-to-box integra más automatización en el picking por lotes. Las áreas de recolección pueden organizarse en estaciones de recolección, cada uno conectado por una cinta transportadora. El selector llena la caja con los productos de los que es responsable y mueve la caja hasta completar el pedido.
Equipo y tecnología de preparación de pedidos de almacén
Otro aspecto clave de la gestión de almacenes es la tecnología que respalda la estrategia óptima para la instalación y la naturaleza del negocio. Por ejemplo, una empresa con un número bajo de SKU y menos líneas seleccionadas puede emplear un método de selección de pedidos individual, y aproveche la tecnología pick-to-belt o elija desde un palet. Las empresas con una gran cantidad de SKU que mueven grandes volúmenes pueden optar por la selección por lotes y la tecnología de voz o pick-to light.
Al considerar qué equipos y tecnologías son adecuados para su almacén:
-
Alinee la tecnología con la cantidad de SKU y el volumen. Mire la cantidad de líneas que se procesan por día frente a la cantidad de productos. En general, cuanto mayor sea el número de SKU y el número de líneas, mayor es la necesidad de automatización.
-
Empiece por implementar un sistema de gestión de almacenes (WMS). Incluso las operaciones de almacén más simples necesitan algún tipo de sistema de gestión de almacén. Busque la funcionalidad básica de preparación de pedidos para almacenar y realizar un seguimiento de los SKU y la ubicación de los artículos y automatizar la creación de listas de selección a partir de los pedidos de los clientes. Un WMS verificará el pedido de un cliente con el inventario disponible y proporcionará instrucciones en forma de lista de selección. Tiene en cuenta la distribución del almacén, la mano de obra disponible y la ubicación del equipo para maximizar la eficiencia y garantizar la precisión en la preparación de pedidos.
-
Integre alguna forma de tecnología de picking móvil. Desde los escáneres de RF móviles básicos, a tecnologías que dirigen las selecciones iluminando botones en los estantes en una ruta de selección (pick-to-light) o guían un selector con auriculares por voz (pick-to-voice), hay muchas tecnologías móviles que son esenciales para una preparación de pedidos precisa, guiar a los usuarios al pasillo exacto, estante, o bin en la ruta más lógica. Asegúrese de que las tecnologías utilizadas en el piso puedan comunicarse fácilmente con el WMS para que no introduzca una complejidad innecesaria.
-
Asegúrese de que el WMS esté integrado con el sistema ERP. El seguimiento del movimiento y las mercancías en el almacén proporciona una gran cantidad de datos valiosos para otros departamentos, como compras o servicio al cliente. Asegúrese de que estas otras funciones tengan acceso a los mismos datos dentro del software que utilizan para sus trabajos.
-
Seleccione el sistema de manipulación de materiales adecuado y ajuste los sistemas a medida que aumentan los SKU y el volumen. Un aumento en el número de SKU requiere mucha más logística en el almacén. Con SKU bajos y volumen bajo, un sistema de manipulación de materiales simple como las carretillas elevadoras puede hacer, pero a medida que aumentan el volumen y la complejidad, la empresa necesitará más mecanización. El equipo de manipulación de materiales es un espacio innovador que aprovecha muchas ideas y tecnologías innovadoras.
-
Considere los avances en el equipo para permitir la configuración de pasillos estrechos. La optimización del espacio disponible en el almacén ofrece ventajas más allá del almacenamiento:también puede ayudar a reducir el tiempo de viaje en el proceso de preparación de pedidos. Los pasillos de los almacenes convencionales tienen de 12 a 14 pies de ancho. Los pasillos estrechos son típicamente de 8 a 10 pies, pero puede medir tan solo seis pies. Combinando las tecnologías y equipos adecuados, Los almacenes pueden lograr ganancias en la preparación de pedidos con pasillos más estrechos.
-
Maximice el espacio del almacén utilizando el equipo adecuado. La tecnología de las carretillas elevadoras mejora constantemente, y hay camiones capaces de atravesar pasillos estrechos y espacios reducidos, como la carretilla elevadora articulada. Amazon aprovecha los robots que se asemejan a las aspiradoras Roomba. Estos robots transportan los artículos necesarios de los estantes al recolector y los empujan hacia lugares estrechos cuando se recuperan todos los artículos.
-
Implementar tecnología transportadora. Existen docenas de tipos de tecnología de transportadores que se pueden utilizar para una recolección más eficiente, así como la salud ergonómica de los empleados que realizan el trabajo.
-
Observe los avances en las tecnologías de clasificación. Combinado con transportadores, Las tecnologías de clasificación proporcionan un aumento de la precisión y la eficiencia, lo que reduce los plazos de entrega y aumenta la precisión.
-
Descubra qué almacenamiento es adecuado para la empresa y no pase por alto los beneficios de las tecnologías automatizadas. Un carrusel por ejemplo, Automatiza el picking mediante una estantería que gira a lo largo de un carril para llevar los artículos al recolector. Se pueden configurar según el método de picking elegido por la empresa.
-
Comprenda todas las opciones de tecnología de recolección automatizada disponibles. Algunas empresas tienen mucho éxito con equipos pick-to-light o pick-to-voice. Con pick-to-light, los recolectores escanean el código de barras de un pedido y se enciende la cantidad y la ubicación del artículo. Pick-to-voice guía al selector y proporciona confirmación a través de un auricular. Hoy dia, Las tecnologías de realidad aumentada están permitiendo avances como las gafas inteligentes para elegir, que muestran la ubicación y la cantidad de un artículo de forma digital a través de unos auriculares portátiles. Proporcionan instrucciones guiadas por voz y la capacidad de escanear directamente con el auricular, lo que permite que el trabajador use ambas manos y maximice la eficiencia con menos toques.
-
Implementar tecnologías inteligentes. Las tecnologías de IoT pueden ayudar a generar recuentos de inventario en tiempo real, mientras que el avance de la tecnología de los dispositivos portátiles, como las gafas inteligentes, facilita el seguimiento del movimiento del inventario y garantiza que el recuento correcto esté ahí para empezar. Esto le ahorra tiempo al recolector y la frustración de buscar artículos que no están allí.
-
Explore el potencial de los robots recolectores. Los robots recolectores realmente pueden hacer la recolección, con la capacidad de alcanzar estantes altos y buscar artículos para empacar, mientras que también está equipado con sensores que evitan que choquen con personas o estantes.
-
Conozca a los co-bots. Los co-bots pueden ser útiles para implementar tareas que tienen cierta repetición, pero también requieren algún nivel de intervención humana. El co-bot puede armar la caja, por ejemplo, o recuperar artículos con una forma o un peso predecibles, como una caja de zapatos.
Mejores prácticas y estrategias de preparación de pedidos en almacén
El diseño del almacén, Los métodos y tecnologías de preparación de pedidos ayudarán a determinar cuál de las siguientes estrategias tiene más sentido implementar para mejorar sus procesos de preparación de pedidos.
Empiece con un objetivo claro sobre lo que quiere mejorar y cómo lo medirá, luego seleccione los consejos que tengan más sentido.
-
Pregunte a las personas que trabajan en el almacén dónde están los cuellos de botella. No olvide las muchas personas que a menudo apoyan sus procesos, incluidos los administradores de la oficina, operadores de equipos y otros.
-
No base los objetivos de preparación de pedidos en promedios. La estacionalidad y las tendencias económicas afectarán en gran medida la forma en que el inventario entra y sale del almacén. Mira los picos y valles, aplicar estadísticas y utilizar algoritmos para determinar objetivos razonables.
-
Seguimiento de la productividad del recolector. Conocer los niveles de productividad permite al gerente del almacén diseñar turnos de acuerdo con la mejor manera de dividir el trabajo. Mire las selecciones promedio por persona-hora, así como a la inversa, promedio de horas-persona por selección. El trabajo promedio por pedido es entonces el número promedio de líneas de picking por pedido multiplicado por el promedio de horas-persona por picking.
-
Mida y mejore el tiempo total del ciclo de la orden o el tiempo del ciclo de la orden interna. La preparación de pedidos es una gran parte del cálculo del tiempo total que se tarda en procesar un pedido. El seguimiento de este número proporciona una medida de la eficiencia del picking.
-
Observe la precisión del recuento de inventario por ubicación y elija las fallas de ubicación (como falta de existencias / pedidos pendientes). Esto indica que no hay una cantidad suficiente en la ubicación designada.
-
Mida la tasa de cumplimiento (por línea y pedidos) para comparar los artículos enviados ese día con el total de artículos pedidos ese día. La tasa de llenado es una buena manera de asegurarse de que las operaciones del almacén satisfagan la demanda de los clientes y, por lo general, se calcula a diario.
-
Mida la precisión de la preparación de pedidos. La precisión en la preparación de pedidos es el número tres en los puntos de referencia más importantes para los almacenes en el informe de evaluación comparativa de medidas de CC de 2020. Una baja precisión en la preparación de pedidos apunta a la necesidad de procesos más eficientes, mejores estándares de control, formación más profunda y más.
-
No olvide los KPI que miden la productividad de los empleados. Estos incluyen líneas despachadas recogidas por hora, líneas despachadas por horas directas, líneas despachadas por horas totales del centro de distribución (DC), horas totales anuales de CC / costo total de CC y costo de CC por mano de obra total utilizada.
-
Seleccione no más de seis puntos de referencia, métricas de focalización que ayudarán a administrar el almacén de manera más eficiente y comparar la eficiencia de múltiples instalaciones.
-
Revise el espacio de su almacén cada vez que realice su conteo físico. Un almacén de bienes de consumo de rápido movimiento deberá actualizarse al menos cada cinco años, a medida que cambian las gamas de productos, los apetitos de los consumidores y las fuerzas económicas más amplias. No evolucionar el diseño del almacén dificultará las estrategias y mejoras de preparación de pedidos.
-
Practique el recuento cíclico para eliminar la complejidad y el desperdicio de SKU.
-
Técnicas como el análisis de inventario ABC (de los cuales hay diferentes tipos) permiten a las empresas clasificar y organizar SKU y eliminar o mover productos que obstruyen sus operaciones.
-
Mire más allá de la clasificación de SKU solo por volumen en dólares, pero también cómo cada SKU consume recursos como mano de obra y espacio. Clasifique los SKU por la cantidad de veces que fueron seleccionados durante un cierto intervalo, rentabilidad, o dificultad en la fabricación, por ejemplo.
-
Implementa algunos principios lean. Realice caminatas regulares de Gemba, dedicando tiempo a observar los procesos del almacén y comprender realmente cómo se completan, para identificar las ineficiencias en las instalaciones. Las empresas también pueden implementar técnicas de poka-yema, donde hacen sus operaciones a prueba de errores y buscan formas de evitar errores involuntarios. Un ejemplo aquí es observar cómo el cross-docking puede mejorar el flujo en el almacén.
Sugerencias para la preparación de pedidos de almacén
Una vez que el personal del almacén sepa dónde centrará la empresa sus esfuerzos, puede comenzar a implementar los siguientes consejos para aumentar la eficiencia y precisión y mejorar la seguridad de los trabajadores.
-
Almacene SKU populares juntos. Se puede aumentar la densidad de púas, al menos a nivel local, almacenando los SKU más populares juntos. Luego, los preparadores de pedidos pueden hacer más selecciones en un área pequeña, reduciendo la cantidad de espacio que necesitan cubrir y aumentando la productividad.
-
Preste mucha atención a las ranuras del producto. El posicionamiento se refiere a la colocación cuidadosa de cajas individuales dentro del almacén, de modo que tipos similares de inventario se almacenen juntos. Se pueden agrupar por tamaño físico, artículos que a menudo se ordenan juntos, estacionalidad y más. Al colocar correctamente el producto, las organizaciones pueden lograr hasta un 30% de ahorro en mano de obra y también garantizar una mejor ergonomía en el almacén, Supply Chain Secrets dice. Clasifique según el volumen y el movimiento y revise la estrategia una o dos veces al año. Un WMS puede ayudar a identificar las estrategias de asignación adecuadas y hay muchos algoritmos que pueden ayudar aquí.
-
Lote de pedidos de una sola línea. Los pedidos de una sola línea son pedidos de clientes de un solo artículo. Por esta razón, no requerirán clasificación al final de una ruta de selección y puede aumentar la eficiencia si un recolector obtiene la mayor cantidad posible de ellos en un solo viaje.
-
Equilibre la reposición de existencias y la recolección para asegurarse de que los artículos estén allí. Supply Chain Secrets dice que una regla general es un reabastecimiento por cada cinco recolectores, pero eso depende de los patrones particulares de flujo. Algunas veces, los almacenes cometen el error de medir los productos solo por los ingresos por ventas, cuando deben mirar el movimiento del producto, teniendo en cuenta el volumen y las ventas.
-
Asegúrese de que el papeleo correcto esté asociado con el pedido correcto. Una quinta parte del tiempo de un selector de almacén se dedica a asegurarse de que el papeleo sea correcto, según Georgia Tech. Esto se puede aliviar enormemente implementando escáneres de RF, que automatizan el proceso y garantizan la precisión al imprimir el albarán del pedido.
-
Estructura de listas de selección para un embalaje eficiente. Piense en cómo encajarán mejor los artículos en la caja en la que se enviarán. Un WMS puede secuenciar las selecciones en una lista de selección para que los artículos grandes se escojan primero, por ejemplo.
-
Maximice la densidad de aciertos. Una forma de hacer esto es aumentar la densidad de picos, minimizar la distancia entre picos para aumentar el número de picos por lugar y, a su vez, aumentar la productividad.
-
No mezcle varios SKU en las mismas ubicaciones. Muchos almacenes todavía tienen una ubicación de contenedor que está vinculada solo a un nivel de estante que contiene hasta diez SKU diferentes. Eso requiere que el empleado busque en varios productos el artículo correcto.
-
Trate de minimizar los toques de los productos. En la mayoría de los almacenes, de siete a ocho personas, desde la entrada hasta la salida hasta la gestión del almacén, tocan un artículo, pero las mejores empresas de su clase tendrán tan solo tres o cuatro toques. Una forma de minimizar los toques es que los selectores seleccionen los artículos y los pongan directamente en la caja de envío, no contenedores de plástico en un carro.
-
Integre las medidas de peso con WMS. Las empresas que envían artículos grandes y pesados pueden aumentar la precisión en la preparación de pedidos al vincular la información sobre el peso del artículo a la lista de selección. Si la elección es, por ejemplo, una unidad corta, el sistema notificará automáticamente al trabajador que el peso es demasiado bajo y le indicará que agregue una unidad más.
-
Elija de la pila del piso. Una estrategia de ranurado de productos es permitir que los selectores seleccionen artículos de alto giro de las cajas de cartón en paletas en el piso utilizando una transpaleta o transpaleta. Esto puede ser más eficiente que mantener estos artículos de venta rápida en estanterías para palés altos.
-
La gente debería elegir utilizando carruseles horizontales en lugar de elevadores verticales. Múltiples esfuerzos de evaluación comparativa a lo largo de los años han demostrado que cuesta más seleccionar verticalmente que horizontalmente. Pero la utilización de la capacidad del almacén exige que las cosas también se almacenen verticalmente. Haga que los artículos de menor velocidad se recojan del almacenamiento vertical y mantenga los artículos de alta velocidad al nivel del piso.
-
Elija de un área de selección rápida o avanzada. Las empresas están diseñando áreas de su almacén para albergar SKU populares que se encuentran en el nivel del suelo y se reponen con existencias de otras áreas del centro de distribución. Georgia Tech dice que el área de picking hacia adelante más común es el estante de paletas de la planta baja que se reabastece moviendo las paletas hacia abajo desde niveles más altos. Otros ejemplos son un estante de flujo de cartón reabastecido de almacenamiento a granel, o equipo especializado como un carrusel o un marco en A que se almacena en otro lugar.
Tomar medidas para capacitar y cuidar a las personas que trabajan en el almacén es otra parte fundamental para garantizar la eficiencia, preparación de pedidos precisa y rentable.
-
Asegúrese de que todo el personal del almacén comprenda el razonamiento detrás de la estrategia de gestión del almacén y por qué es importante para el negocio. no solo gerentes. Un gran ejemplo de por qué esto es importante proviene de SI Systems, que señala que cuando muchas empresas implementan la verificación de códigos de barras dobles, donde el operador escanea el SKU del producto y luego el palet, para mejorar la precisión. Sin embargo, En cambio, el operador suele escanear dos veces el palé porque es más rápido. El empleado hace esto porque quiere alcanzar los niveles de productividad o rendimiento y no se da cuenta de por qué escanear ambos es crucial para la precisión del inventario. Debe realizar un proceso de capacitación formal con los miembros del equipo y explicar la justificación comercial de cada parte de un proceso.
-
Utilice métricas reales para establecer estándares de rendimiento realistas para los trabajadores del almacén. Utilice métricas como las líneas de pedido seleccionadas por hora y el costo de selección de cada línea de pedido y busque mejorarlas proporcionando a los selectores las tecnologías adecuadas que facilitarán una mayor eficiencia y precisión. como pick-to-light y pick-to-voice.
-
Fomentar la cooperación. Un panel de control de calidad o un centro de control puede ayudar a monitorear el desempeño general del almacén para recompensar y animar a los equipos. pero busque también resaltar las ganancias individuales de los empleados. Muestre estadísticas de empresas de alto rendimiento e incentive la productividad y el rendimiento de seguridad sólidos.
-
Trabaje para reducir las horas extraordinarias. Compare las horas totales con la producción y observe las líneas de pedido seleccionadas por hora de mano de obra, por ejemplo, para medir la eficiencia laboral. Considere las horas normales trabajadas frente a las horas extraordinarias, líneas recogidas por día y número de cajas, echas o paletas recogidas por período. Compare este período con el período. Si estos números son bajos, pero las horas extras son altas, averigua porque.
-
Tome medidas para hacer que el lugar de trabajo sea más seguro y de conformidad con las normas de OSHA. Las mejores operaciones de almacén cuentan con programas formales de capacitación en seguridad y capacitación continua. Coloque los productos en la denominada “zona dorada” para garantizar una salud ergonómica adecuada. Marque claramente los pasillos y las áreas de trabajo con marcadores de seguridad y manténgalos libres de escombros y peligros. Asegúrese de que los trabajadores del almacén usen todo el EPP adecuado en todo momento, incluidos los cascos, gafas guantes, mascarillas uniformes adecuados y más.
-
Revise y perfeccione los procesos con regularidad. A medida que cambian las estrategias de producto, asegúrese de que la estrategia del almacén también funcione. Los desafíos de la cadena de suministro y los esfuerzos para aumentar la resiliencia de la cadena de suministro desafiarán muchos de los principios de la gestión de inventario justo a tiempo que han guiado las operaciones del almacén durante años. En muchos casos, se necesitará más espacio y es posible que se mantengan existencias durante períodos de tiempo más prolongados para estar preparados para los aumentos repentinos y la escasez. En efecto, la demanda de espacio de almacén es alta:The Wall Street Journal informó que la actividad inmobiliaria industrial aumentó un 43% de abril a mayo de 2020, con demanda de almacenes de más de 100, 000 pies cuadrados siendo el más fuerte.
Optimice la preparación de pedidos con el software de gestión de almacenes
Piense en el pedido del cliente como una lista de compras para que el recolector la cumpla, con cada entrada en la lista (conocida como líneas de pedido) anotando el artículo y la cantidad. Idealmente, Existe un sistema de gestión de almacén para verificar el inventario disponible y dónde encontrarlo. así como reorganizar los pedidos en una lista de selección que tiene en cuenta el diseño del almacén para aumentar la velocidad. El número de líneas de picking puede ser una indicación de cuánto tendrá que viajar el trabajador por el almacén para obtener los artículos necesarios para los pedidos.
Las empresas pueden recurrir a los sistemas de gestión de almacenes (WMS) para ayudar a gestionar los procesos de entrada y salida de sus almacenes y obtener visibilidad de todos los SKU almacenados y su ubicación. La funcionalidad WMS se basa en la de una solución de gestión de inventario, y también tiene capacidades para ayudar con la estrategia de almacenamiento y la gestión de la fuerza laboral. El WMS proporciona detalles sobre todos los artículos en el almacén:dimensiones físicas, cómo está empaquetado, dónde se almacena y la ruta más eficiente para llegar a ellos.
Un WMS admite la programación de citas, recepción, seguro de calidad, almacenamiento seguimiento de ubicación, gestión de órdenes de trabajo, cosecha, embalaje y consolidación y envío. El WMS transforma el pedido de un cliente en una lista de selección y realiza un seguimiento del ensamblaje del pedido. El WMS también puede gestionar los procesos de entrada en un almacén, mostrando dónde debe almacenarse el inventario, seguimiento de la productividad del trabajador, asegurando que los pedidos cumplan con los horarios de envío y más. También puede conectarse a los sistemas ERP y de gestión de pedidos. Específicamente, para la función de picking, un WMS robusto puede admitir pick-to-light, Operaciones dirigidas por RF, planificación laboral, Ranuramiento de SKU y mucho más.
El WMS adecuado se escalará a medida que se necesiten nuevas funciones y se adaptará a medida que cambien los procesos. Si bien el edificio en sí puede permanecer estático, Los procesos y tecnologías de una empresa no deben ser inamovibles. Al observar constantemente los sistemas y cómo las personas los utilizan para realizar su trabajo, la gestión del almacén se puede mejorar constantemente, ayudar a los empleados a hacer su trabajo de manera más eficaz y asegurarse de que los clientes sigan comprando y confiando en su empresa.
Negocio
- Los 11 mejores planes de jubilación:pros y contras
- Cuándo comprar una acción y cuándo vender una acción:5 consejos
- Previsión de inventario:tipos,
- Inventario físico:Pasos,
- Gestión de inventario minorista:qué es,
- 35 métricas de comercio electrónico con fórmulas, Puntos de referencia y consejos
- 51 consejos de gestión de almacenes para su empresa
- Guía definitiva para la preparación de pedidos:tipos, Métodos y consejos
- Los mejores consejos, Trucos, y herramientas para trabajar a distancia
-
Los mejores consejos e información útil sobre cómo operar con criptomonedas
Antes de sumergirse de lleno en el comercio de Bitcoin, Existen numerosos consejos esenciales que necesita si prevé un viaje casi tranquilo en su nueva empresa. Esta no es una promesa de que su estado...
-
¿Es arriesgado comerciar con Altcoins? - Mejores prácticas e información útil
En gran medida, esta pandemia actual ha devastado muchas empresas y sectores financieros, incluido el mercado de las criptomonedas. Aunque Bitcoin ha dominado el mercado de las criptomonedas y registr...